The FLEXline series offers maximum flexibility by the modular design of different configurations as well as extended possibilities for the realisation of special functions.
The adaptation or addition of individual mechanical components is just as possible as special programming or integration into a complete production line.
In addition, various application systems up to hot runner system with different nozzle geometries and arrangements are available.
The melting units can be optimally adapted to the requirements of the respective project with different melting and conveying systems and, in the event of different or changing project requirements, can also be switched at any time by our "plug-and-play" system.
Extensive peripherals and additional options round off the system.
The FLEXline can thus be optimally adapted to the requirements of the respective project.
- For medium to large series productions
- Flexible, project-specific design of the equipment possible
- Extensive special options and peripherals available
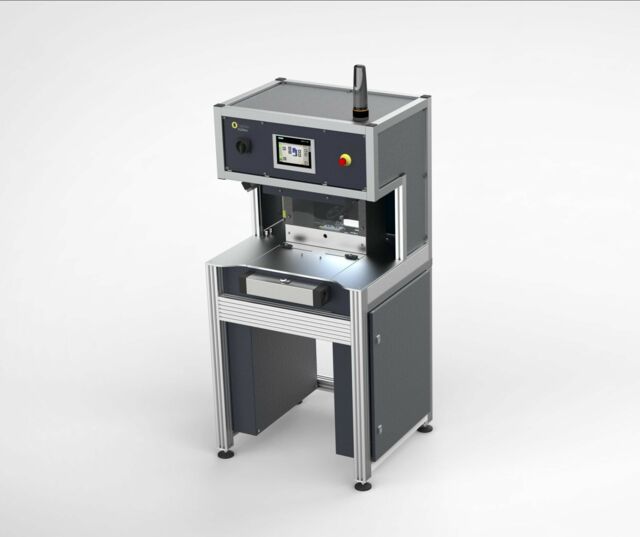
Specifications
Operating temperature: max. 250°C
Melting capacity: 2 – 15 kg/h (depending on the adapted melting unit)
Mass pressure : 0,5-4 MPa/ 5-40 bar
Calmping force: 9 kN / 12 kN / 19 kN / 38 kN
Power connection: 3/N/PE AC 400/50 Hz.
Power consumption: 4,5 kW
Clamping force of 9-38kN for components up to approx. 9,500 mm²
Siemens S7 controller with touch panel
Optional machine accessories and peripherals
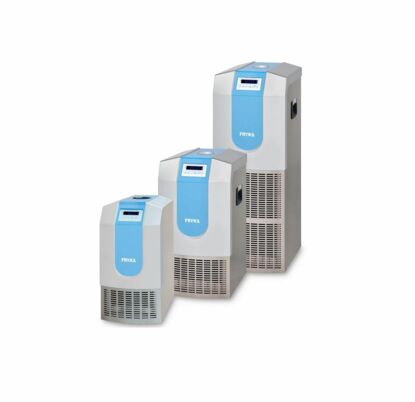
Devices for mold temperature control
Depending on the application, various devices with working ranges from -10°C to + 60°C and flow rates of up to 20l/min are available.
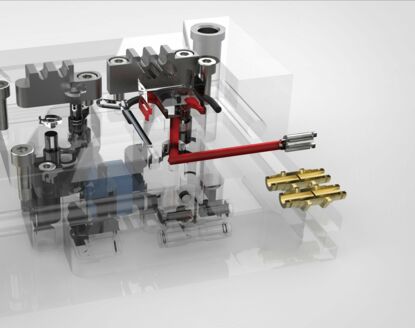
Air nozzles for demoulding
Air pulses in the upper part of the mold to keep the encapsulated components in the lower cavity when the mold is opened.
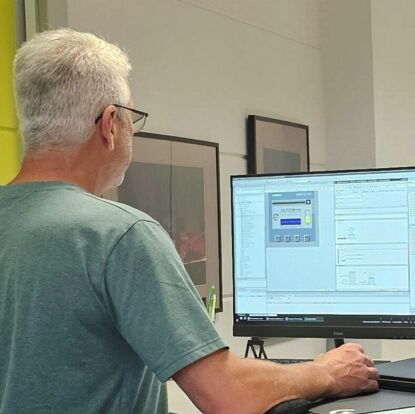
Remote maintenance
Router and ethernet interface with secure and fast access for support in the event of a malfunction or for transmitting program adjustments.
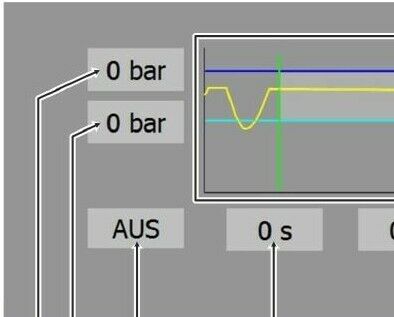
Pressure monitoring for application head
A pressure sensor in the application head measures and monitors the moulding pressure. Print curve display and archive in machine PLC.
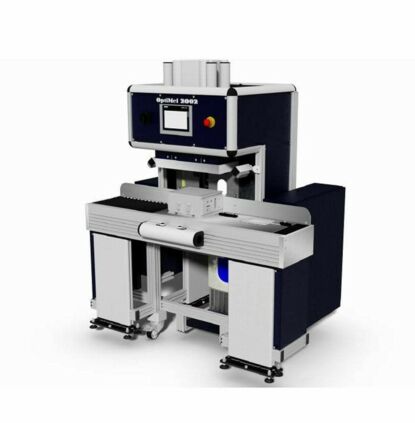
Height adjustment
Allows electrically controlled, stepless adjustment of working heights.
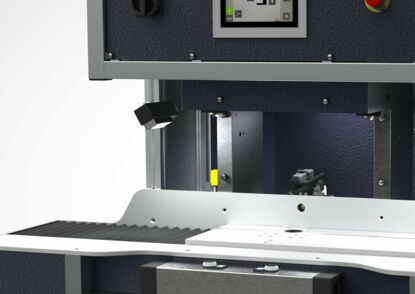
Lights for work area
For additional illumination of the handling area.
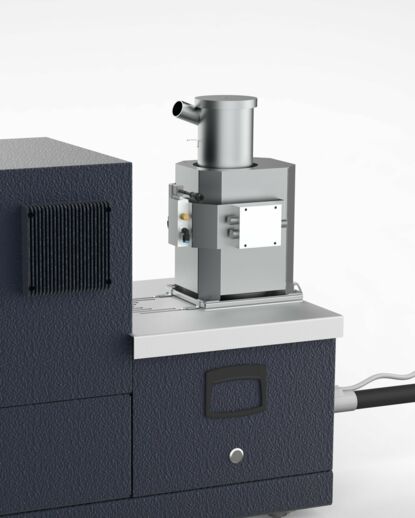
Automatic filling
Conveyor unit for automatic refilling of the melting tank, incl. sensor for monitoring the fill level as well as storage container for the granulates.
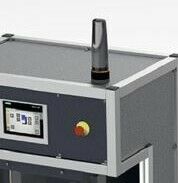
Signalling column
Indication of the operating status by five segments in different colors and light modes.
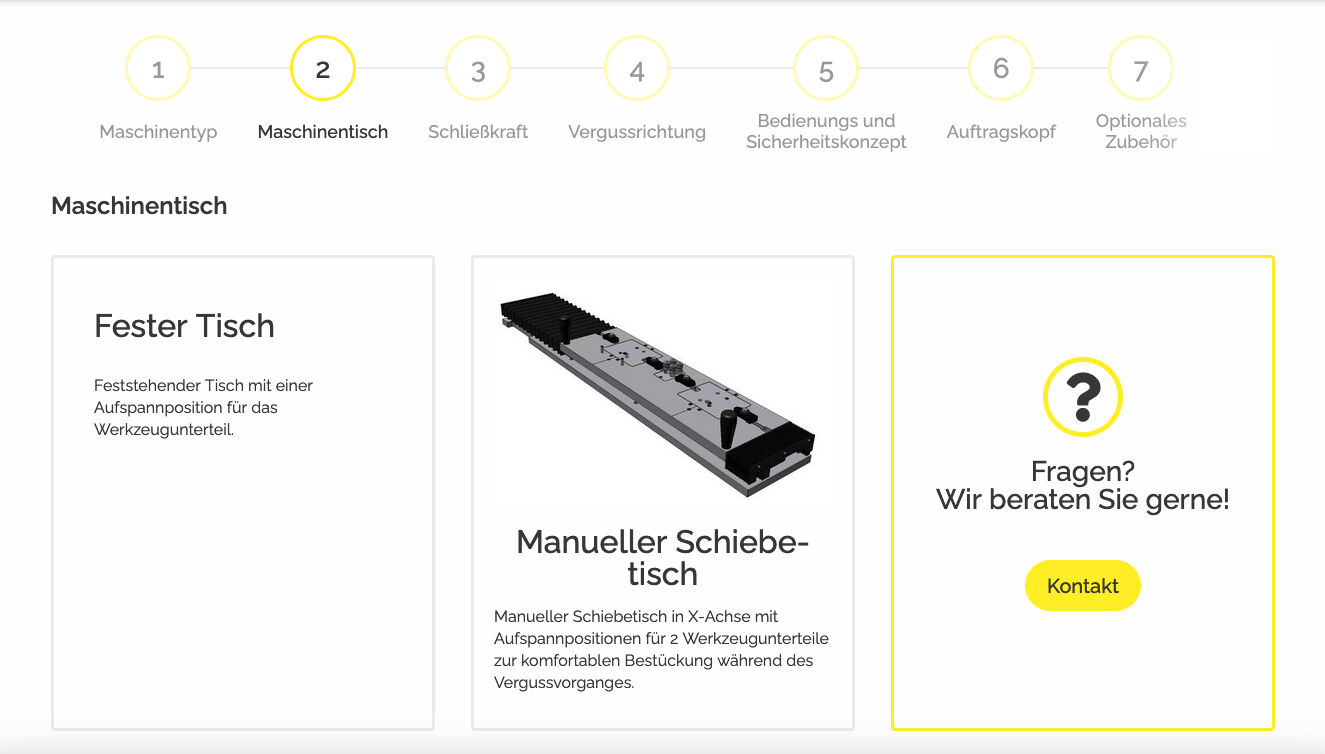
Machine configurator
Use our machine configurator to put together your individual Low Pressure Molding FLEXline machine, tailored to your manufacturing processes.
Low Pressure Molding tools
The decisive factor for the technical implementation of any project is the corresponding moulding tool. Each is individually developed, designed and manufactured for the respective project.
Our experienced designers and project managers are always available to consult you!
Hot melts for electronics encapsulation
There is the right material for every application. Amongst our hotmelt granulates we also have the right material for special projects and areas of application.
Find out more about the various types of materials.
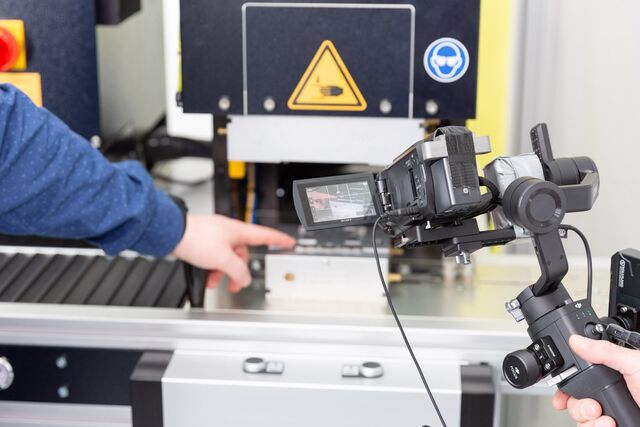
Virtual LPM Studio
With our OptiMel Studio, we added a digital space to our facilities in 2020.
We are thus just as well positioned for virtual trade fairs and lecture events as we are for individual online seminars and training courses.
In addition, individual consultation appointments can also be organised. For example, you can get to know our machine system in detail, book operator and maintenance training courses or take part in a tool sampling - and all this conveniently from the comfort of your own workplace.
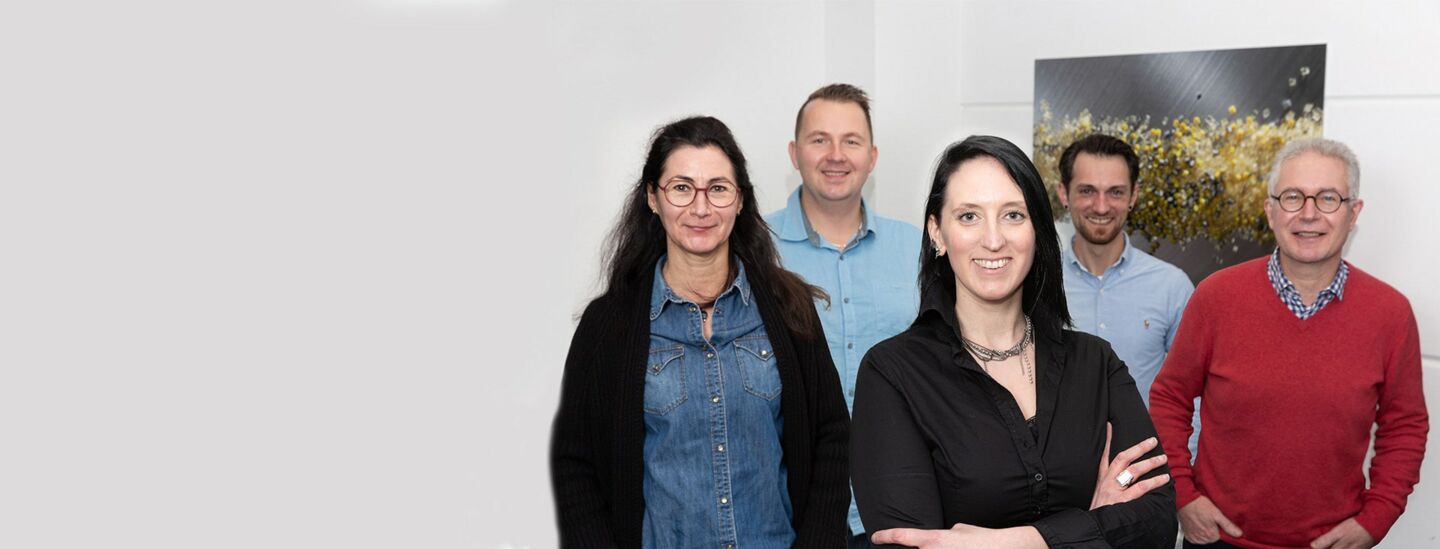
Do you need support in choosing the right equipment? Would you like advice on individual solutions?
We are at your disposal!