Our hotmelt machine system
Our aim is to supply the matching equipment for every project and to constantly expand the possibilities in the application field of the Low Pressure Moulding technology.
Our many years of experience as a hot melt machine manufacturer has enabled us to continuously develop our systems to meet ever demanding project requirements.
Individual configurations for the construction of a Low Pressure Moulding machine can be selected and combined according to the respective project and production requirements.
We have said goodbye to the "standard" and instead defined three hotmelt machine series, which make everything possible, from high-performance basic options, individual special adaptations to completely customised designed solutions.
New innovative concepts can also be invented based on the existing Low Pressure Moulding System and integrated into the process.
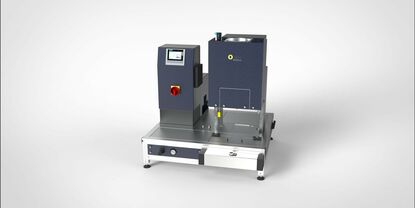
BASEline
The BASEline series combines compact design with convenient operation and offers optimal possibilities for small to medium shot weights and/or quantities.
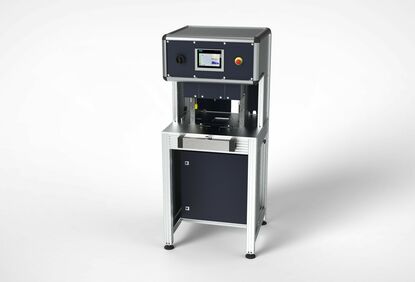
FLEXline
The FLEXline series offers maximum flexibility in terms of design and peripherals. Project-related adaptations of individual components are just as possible as special programming or integration into a production line.
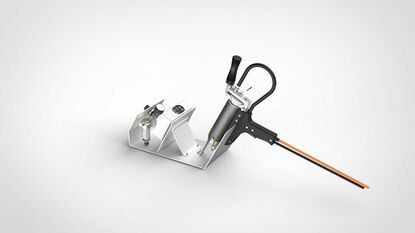
LABline
Many projects and new processes start with prototypes, pre-series and small series. For this purpose, the LABline offers manual devices that are specially adapted to the requirements of Low Pressure Moulding.
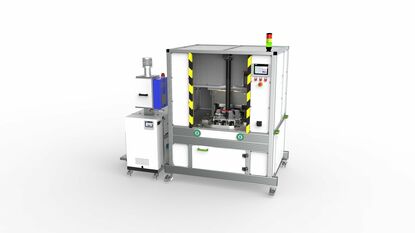
CUSTOMline
In addition to the flexibility of the modular system, we implement complete custom-made systems. Components from the other series can be used and combined with individually designed solutions.
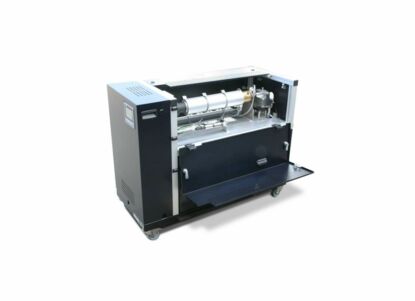
Hotmelt Extruder
The special system combines the advantages of an extruder with the requirements of the Low Pressure Moulding technology.
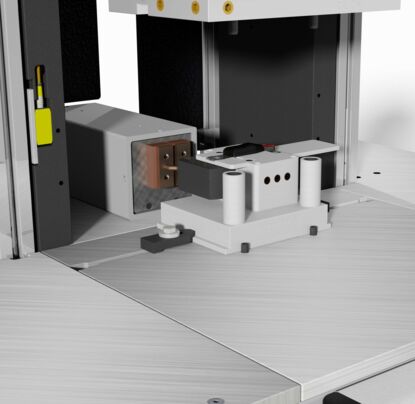
Hotmelt Induction
Integrated induction equipment enables reliable and efficient adhesion to metallic components.
Our LPM machine configurator
Create your Low Pressure M0ulding machine with our Optimel machine configurator. For every individual requirement, you are guaranteed to find the right machine for your production process.
Choose freely, e.g. between machine type, moulding direction and melting device and thus put together your individual machine conveniently and easily yourself. You can then send us your machine concept directly so we can support you with a consultation.
Machine type
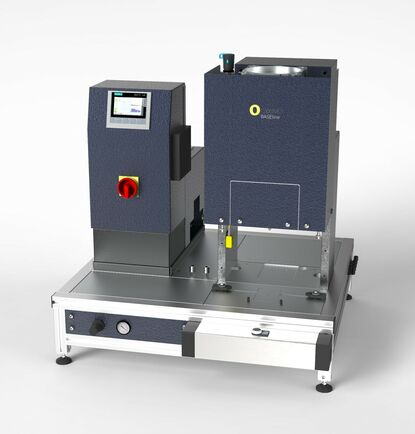
Machines for small to medium-sized series productions. Adapted melting unit with double-acting piston pump and a melting capacity of approx. 1kg /h for small to medium shot weights and / or quantities. Clamping force of 9 / 12kN for moulding surfaces up to approx. 3000mm² (at a maximum pressure of 40 bar).
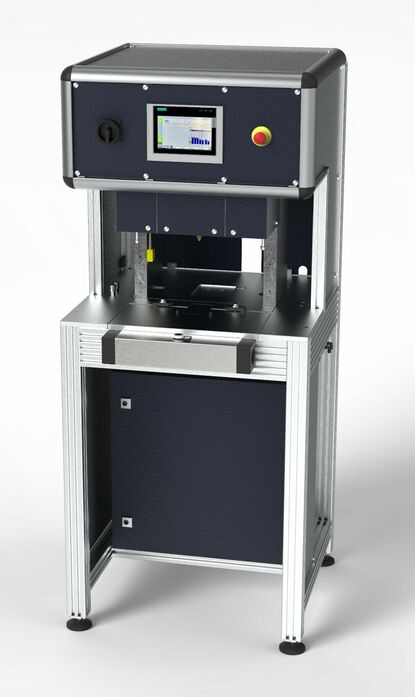
Machines for medium to large series production. Flexible, project-specific combination of machine components. Melting performance for medium to large shot weights and / or medium to large annual quantities. Clamping force for components with a total moulding surface of up to approx. 9,500mm² (at a maximum pressure of 40 bar.

Device for manual production of samples and prototypes. The maximum processing temperature of 250 ° C allows processing of all Technomelt® products.
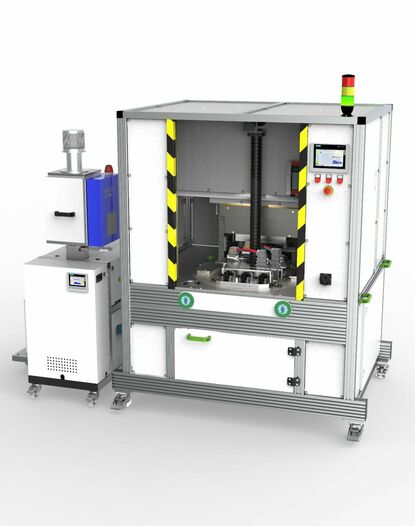
Individual special machines based on the respective project and production requirements.
We are happy to help!
Machine table
Fixed table with one clamping position for the lower tooling part.
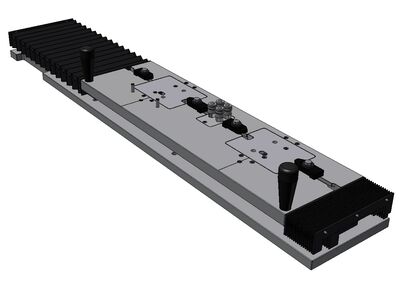
Manual table in X-axis with clamping positions for 2 lower tooling parts for convenient handling during the moulding process.
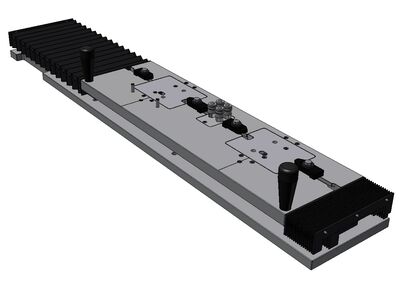
sliding table
Pneumatic operating sliding table in X-axis with clamping positions for 2 lower tooling parts for convenient handling during the moulding process.
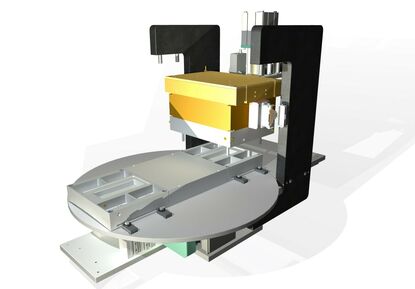
Rotary table with clamping positions for 2 lower tolling parts and 180° rotation. Automatic assembly outside of the potting position is also possible.
We are happpy to help!
Clamping force
For components with a maximum moulding surface of up to approx. 2,000mm² (at a maximum pressure of 40 bar).
For components with a moulding surface of up to approx. 3,000mm² (at a maximum pressure of 40 bar).
For components with a moulding surface of up to approx. 5,000mm² (at a maximum pressure of 40 bar).
For components with a moulding surface of up to 9,500mm² (at a maximum pressure of 40 bar).
We are happy to help!
Application orientation
We are happpy to help!
Operation and safety concept
Manual clamping system with pneumatic support and locking during the moulding process.
The pneumatic clamping unit is controlled via two-hand operation. In combination with a downstream safety valve, an operating and safety concept is created for a one-person workplace.
The work area towards the operator is secured by a light curtain. Intervening while the clamping unit and sliding table are moving leads to a stop. In combination with a capacitive start button and safety valve, a safe and convenient concept.
The work area towards the operator is secured by a light curtain. Intervening while the clamping unit and sliding table are moving leads to a stop. In combination with a capacitive start button and safety valve, a safe and convenient concept.
The safety concept of the Baseline series with light barrier is designed for tools with a maximum depth of 130mm and a parting line at the maximum height of 60mm.
Tools that exceed these dimensions must not be used.
We are happy to help!
Application head
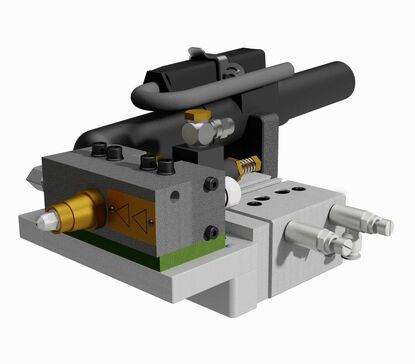
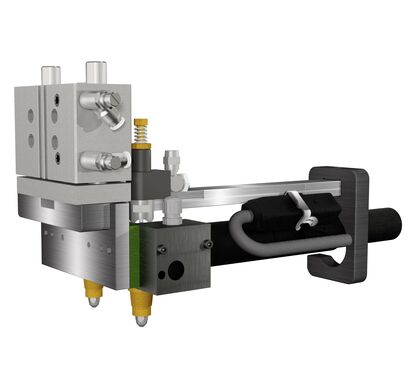
For moulding with multiple cavities or multiple runner points for larger components.Different nozzle width available.
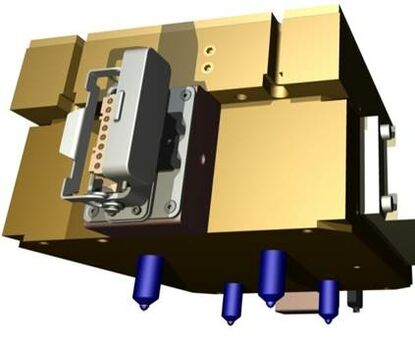
Hot runner system with project-specific number and arrangement of heated nozzles.
We are happy to help!
Melting units
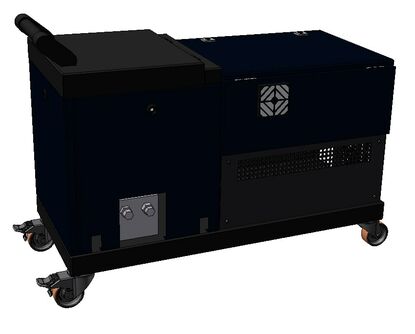
Device with gear pump and 4 liter tank with melting capacity of up to 12kg per hour (depending on material). Also available with enlarged tank with 12 liter filling volume.
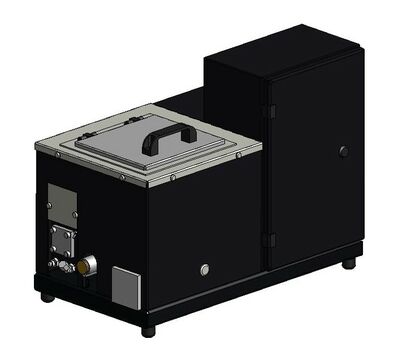
System with a choice between gear and plunger pump as well as 2 tank sizes with 2 and 7 liters and a melting capacity of 4-6kg per hour (depending on the material).
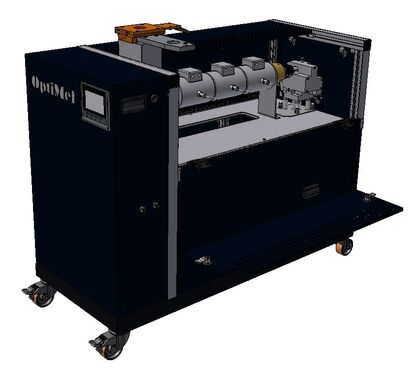
Material-friendly processing with extruder screw and 5 separately controllable heating zones. Filling via a specially developed plunger unit. By decoupling the injection process, a melting capacity oc approx. 5kg/h can be achieved and the occurrence of pressure peaks can be avoided.
We are happy to help!
Optional equipment
Depending on the application, various devices are available with working ranges from -10 ° C to + 60 ° C and delivery rates of up to 20l / min.
For air impulses in the upper part of the tool which hold the mouldedcomponents in the lower cavity when the tool is opened.
Router and Ethernet interface for safe and fast access to provide support in the event of a fault or to be able to transfer program changes.
A pressure sensor in the application head measures and monitors the moulding pressure. Pressure curve display and archive in machine PLC.
Enables an electrically controlled, continuously variable adjustment of the working height.
Capacitive sensor for monitoring the fill level in the melting tank. Message in the control panel when refilling is necessary.
Delivery unit for automatic refilling of the melting tank. Including sensor for monitoring the fill level and storage container for the granulate.
Replaces the pushbuttons for increased ease of use.
For additional illumination of the handling area.
We are happy to help!
Equipment
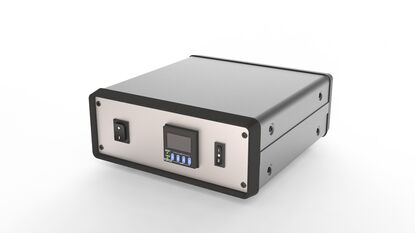
For control of a fixed moulding time for increased process reliability even with manual moulding.
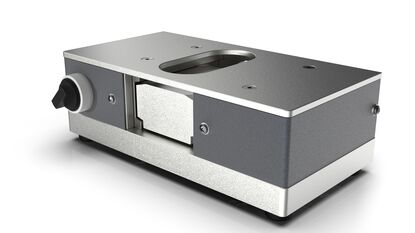
Two pneumatically controlled clamping jaws fix small sample tools for manual moulding.
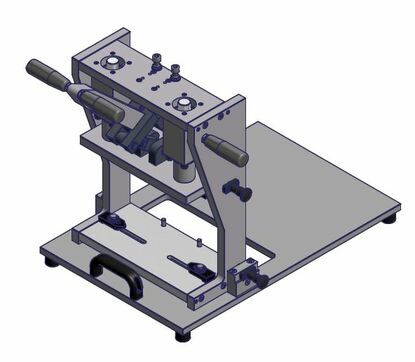
The manual toggle system enables serial tools to be processed with the manual application device.
We are happy to help!
Unsere Service- und Zusatzleistungen
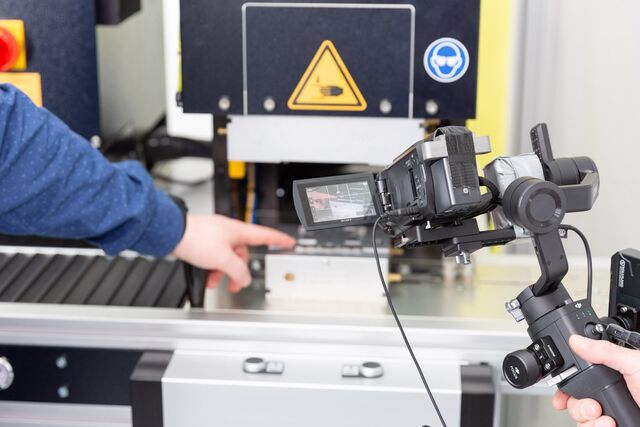
Virtuelles LPM Studio
Mit unserem OptiMel Studio haben wir uns im Jahr 2020 um einen digitalen Raum erweitert.
Für virtuelle Messen und Vortragsveranstaltungen sind wir damit ebenso gut aufgestellt wie für individuelle online-Seminare und – Schulungen.
Darüber hinaus können auch einzelne Beratungstermine organisiert werden. So können Sie z.B. unser Maschinensystem im Detail kennen lernen, Bediener- und Wartungsschulungen buchen oder an einer Werkzeugabmusterung teilnehmen – und das komfortabel und einfach von Ihrem Arbeitsplatz aus.
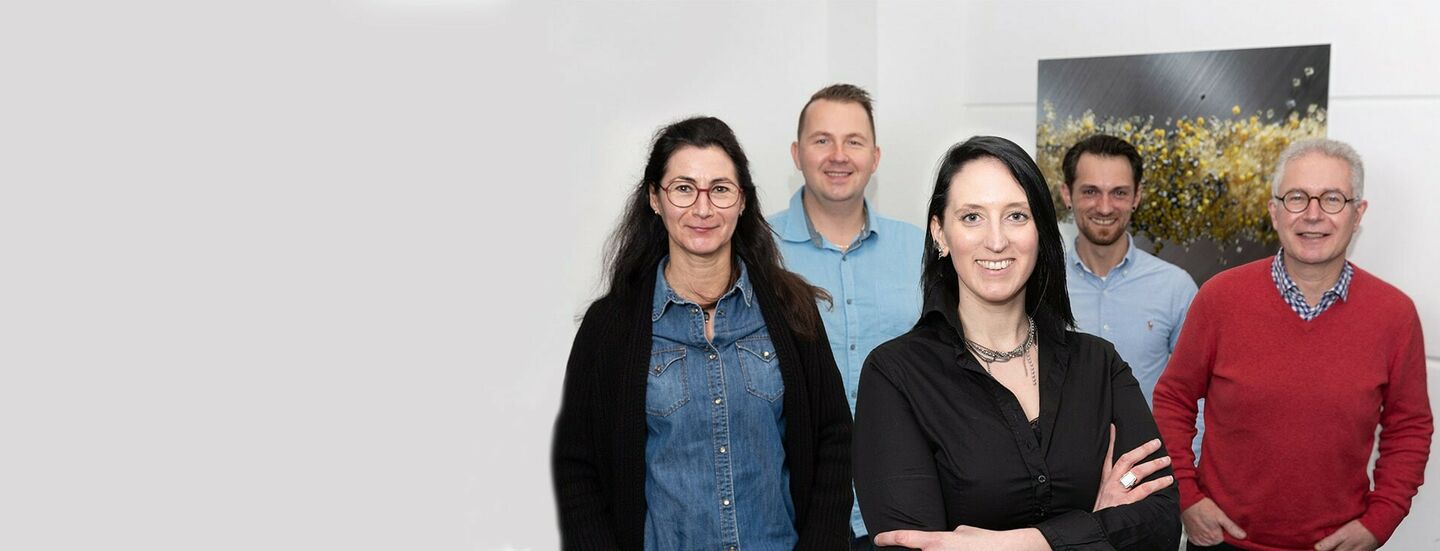
Brauchen Sie Unterstützung bei der Auswahl des passenden Equipments? Möchten Sie Beratung zu individuellen Lösungen?
Wir stehen Ihnen gerne zur Verfügung!