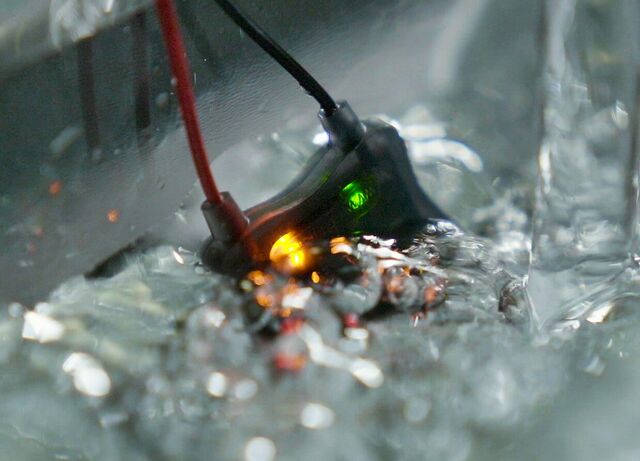
Seinen Ursprung hat das Low Pressure Moulding Verfahren oder auch Hotmelt Moulding Verfahren in der Abdichtung von Kabelsträngen in der Automobilindustrie – heute findet es Anwendung in vielen Bereichen für den Schutz elektrischer und elektronischer Bauteile. Bei 5-40 bar (in Einzelfällen bis zu max. 60 bar) erfolgt die Verarbeitung mit wesentlich niedrigerem Druck als im klassischen Hotmelt Spritzgussverfahren. So ist es problemlos möglich, auch empfindliche Bauteile wie z.B. Leiterplatten, Sensoren etc. direkt zu umhüllen.
Die Zykluszeiten beschränken sich auf den reinen Verguss, der je nach Größe und Kontur der Bauteile bei ca. 10-60 Sekunden liegt. Anschließend ist eine direkte Weiterverarbeitung möglich, was einen deutlichen Zeitvorteil gegenüber z.B. dem 2-K-Verguss bedeutet. Die haftenden Eigenschaften der verwendeten Materialien ermöglichen, bei passender Materialkombination, einen Schutz der Bauteile bis IP68.
Durch einen optimierten Materialfluss kann das Hotmelt Moulding mit den verwendeten Thermoplasten auch bei temperaturempfindlichen Bauteilen realisiert werden. Verschiedene Materialeigenschaften und Verarbeitungsvarianten, die Kombination unterschiedlicher Materialien sowie ggf. weitere Prozessschritte ermöglichen ein breites Einsatzspektrum.
White Paper & Solutions Guide
Erhalten Sie detaillierte, exklusive Einblicke in die Technik des Low Pressure Moulding.
Unser White Paper vermittelt neben Funktionsweise und Anwendungsmöglichkeiten die technologischen Grundlagen und gibt Einblicke in die Entstehung und Entwicklung der Technologie.
Der Solutions Guide fungiert als verlässliche Orientierungshilfe, damit Sie Ihr Vorhaben mit der Low Pressure Moulding Technologie effizient und präzise realisieren können.
Sie erhalten fundierte und erfahrungsbasierte Einblicke in die Welt des Elektronikvergusses mit Low Pressure Moulding.
Sie möchten das White Paper oder den Solutions Guide als kostenloses PDF erhalten, dann nutzen Sie das Kontaktformular und in Kürze erhalten Sie die Datei per E-Mail.
Bis zum Erhalt der kompletten Datei, haben Sie bereits Zugriff auf eine Leseprobe White Paper (6 Seiten).
LPM - das Wesentliche
- Niedrige Drücke
- Kurze Zykluszeiten
- Keine Aushärte-/ Reaktionszeiten
- Gehäuseersatz
- Als Zugentlastung geeignet
- Für temperaturempfindliche Bauteile
- Einsatz-Temperaturen -50°C - + 150°C
- Dichtigkeit bis IP68
- Breites Einsatzspektrum
Gerne organisieren wir für Sie und Ihre Kollegen Technologie-Schulungen zum Kennenlernen der Möglichkeiten und Bewerten der Anwendungsfälle in Ihrem Unternehmen - vor Ort oder online aus dem OptiMel Studio.
Anwendungsbereiche
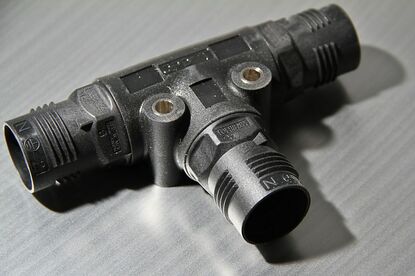
Stecker und Tüllen
Umhausung und Abdichtung auch mit integrierter Zugentlastung und Knickschutz lassen sich für Steckverbindungen und Tüllen realisieren. Eine definierte Lage der Bauteile und ggf. Abdichtung wird durch eine jeweils speziell angefertigte Vergusskavität, Klemmplatten und Gegenstecker im Werkzeug abgebildet.
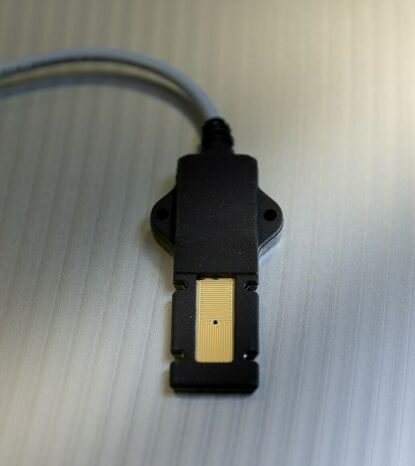
Sensoren
Sensoren werden vor einer Vielzahl äußerer Einflüsse geschützt ohne ihre Funktionalität zu beeinflussen. Sie können komplett umhüllt werden oder es können durch Nutzung der klebetechnischen Eigenschaften der Materialien wichtige Messbereiche vom Verguss freigehalten und gleichzeitig wichtige Elektronik-Bereiche mediendicht geschützt werden. In beiden Fällen werden dank der geringen Drücke des LPM-Verfahrens Bauteilschädigungen vermieden.

Gehäuseersatz
Individuelle Formgebung und Abdichtung in einem Prozessschritt – woraus sich i.d.R. neben den durch die Abdichtung ermöglichten technischen Vorteilen – im Besonderen auch die Möglichkeit höherer Produktionsstückzahlen pro Zeiteinheit und somit deutliche Kosteneinsparungen ergeben.
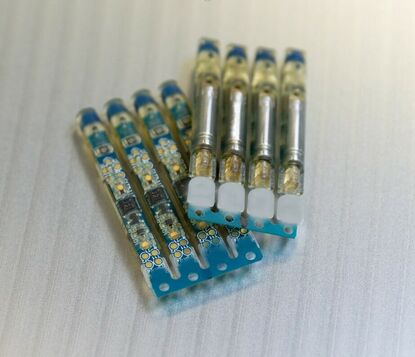
Leiterplatten
Der Verguss dient zum Schutz der Bauteile vor Vibration, Feuchtigkeit, Verschmutzung, Berührung und mechanischer Belastung ohne sie produktionstechnisch zu beeinflussen oder zu beschädigen.
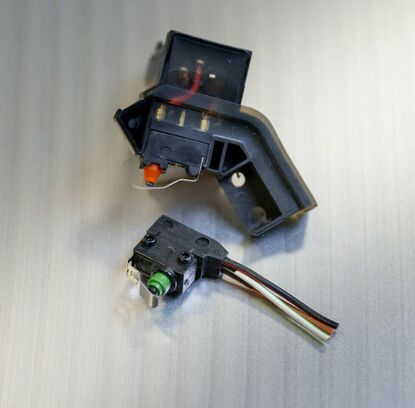
Mikroschalter
Das Low Pressure Moulding kommt hier überwiegend zum Einsatz um durch Schutz vor eindringender Feuchtigkeit eine langfristige Funktionserhaltung zu gewährleisten.
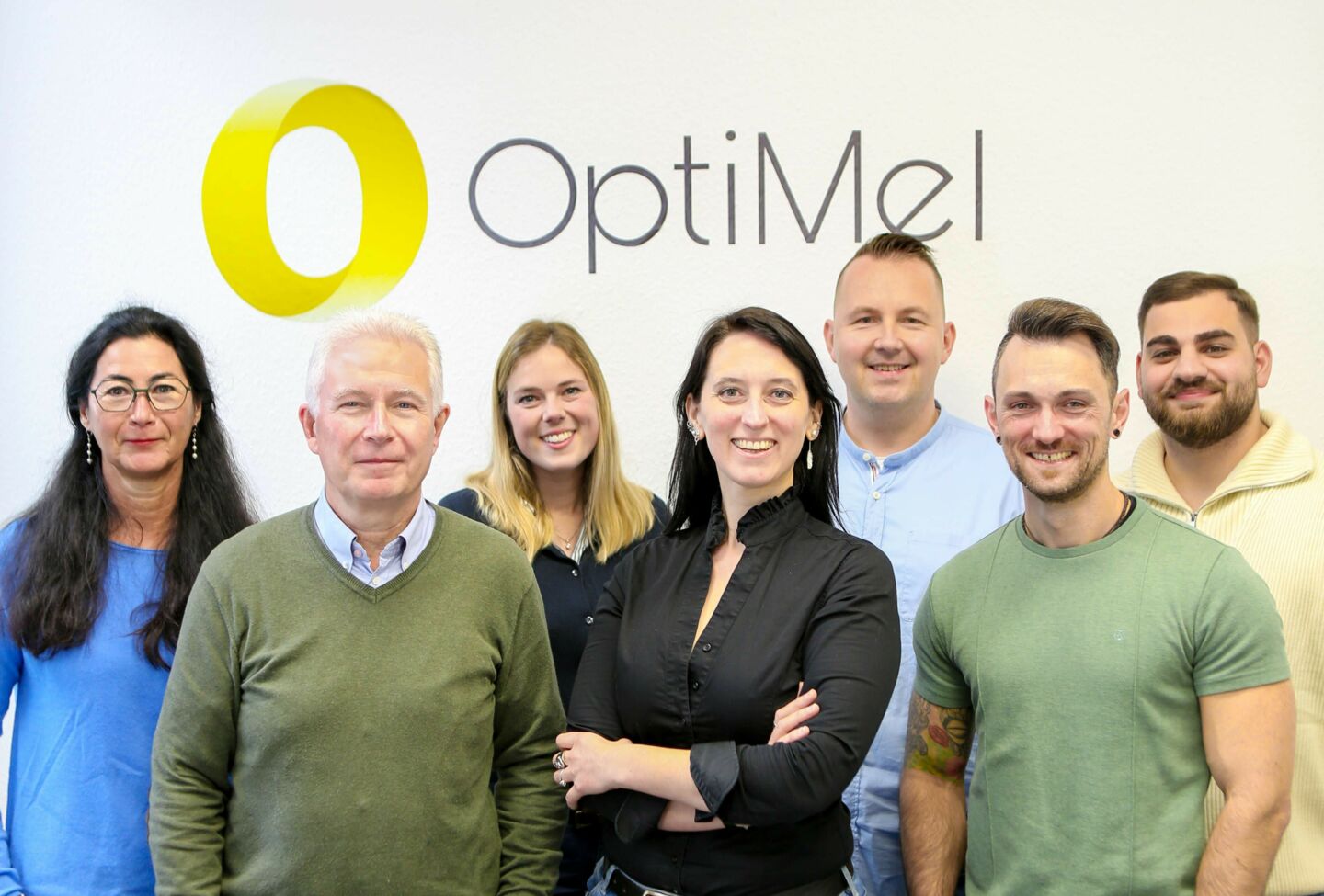
Möchten Sie noch mehr Details zur Technologie erfahren? Haben Sie Projekte, deren Umsetzung Sie mit uns diskutieren möchten?
Wir freuen uns von Ihnen zu hören!